The Raw Material Cost Table is essential to configure and manage the prices of the company's raw materials. In this organized structure, the raw materials are listed with their corresponding values, facilitating the consultation and updating of prices efficiently.
Add a Cost Table
Open the menu on the left side of the screen and select "Administration" - "Raw Material Cost Table."
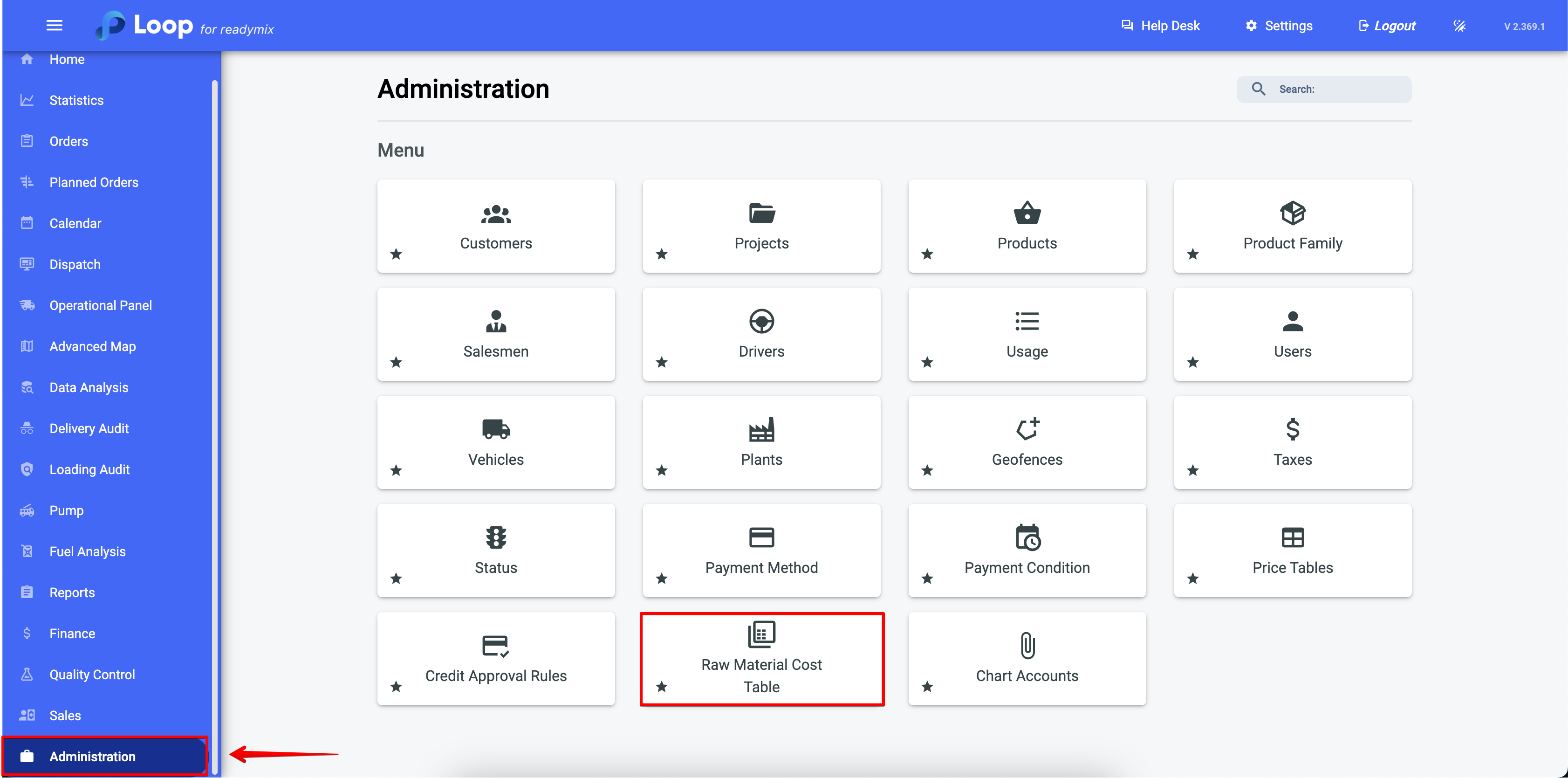
First, click on "Add Raw Material Cost Table" complete the required fields, add raw materials, and set the cost for each of them.
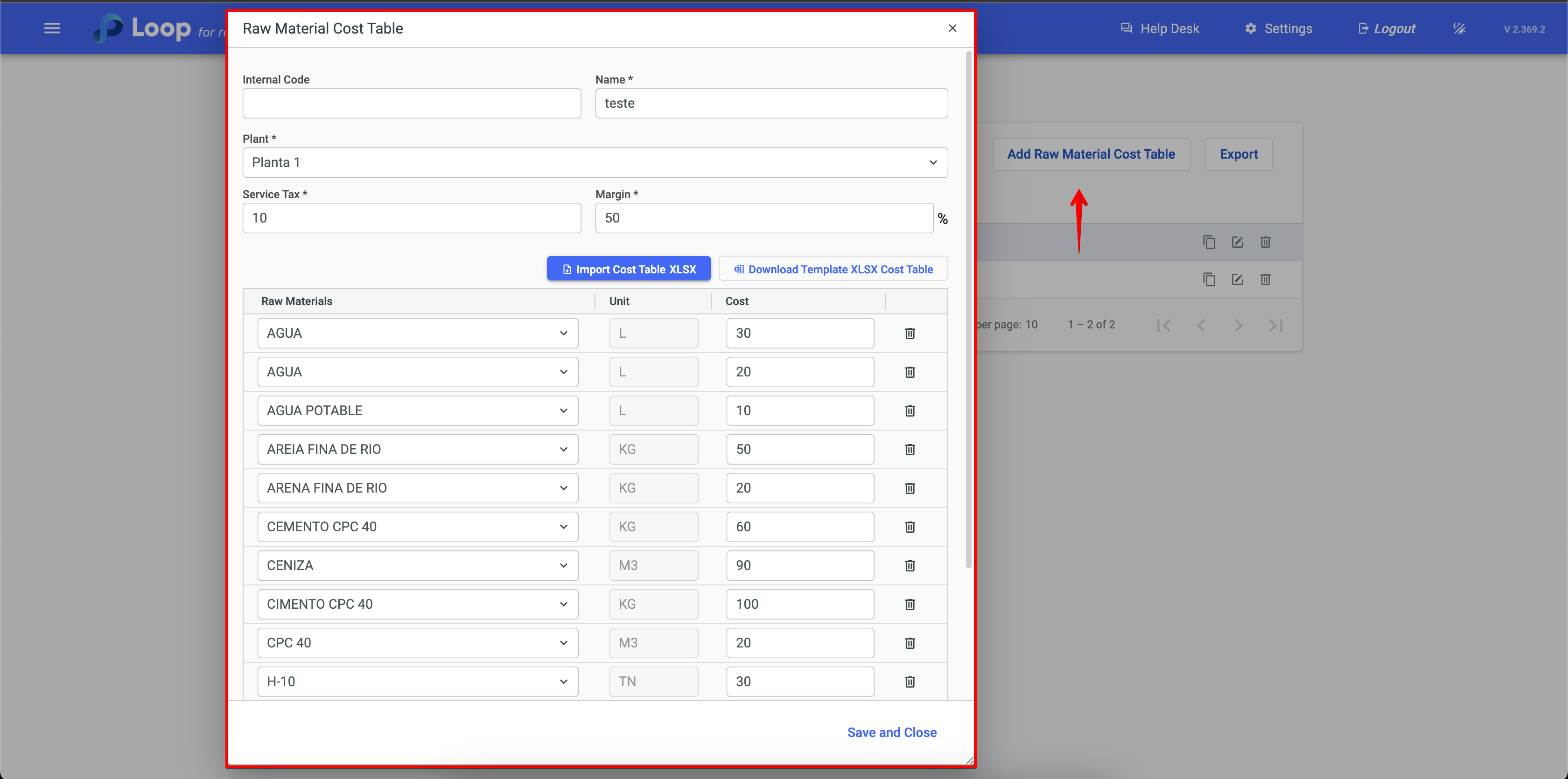
Remove or Add Raw Materials
To remove raw materials, simply click on the trash can icon. If you wish to add more raw materials, use the plus icon.
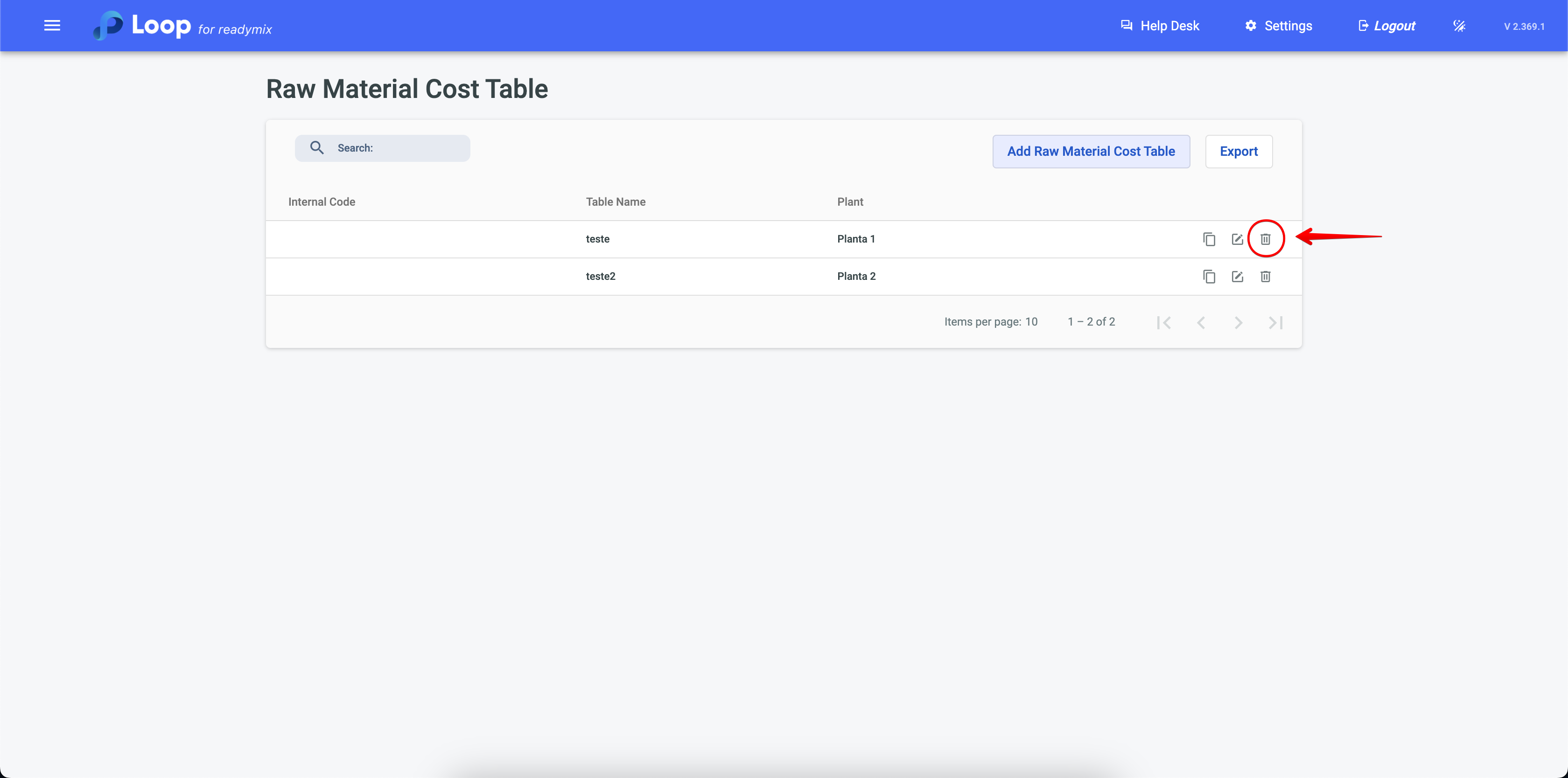
Download Model Table
In the "Example Table" option, you will find two choices: a blank table and another one that contains all the registered raw materials in the system.
You can download a blank spreadsheet in which you can input the costs of raw materials. Later, this spreadsheet can be used to automatically calculate the product price based on the costs of the raw materials you entered.
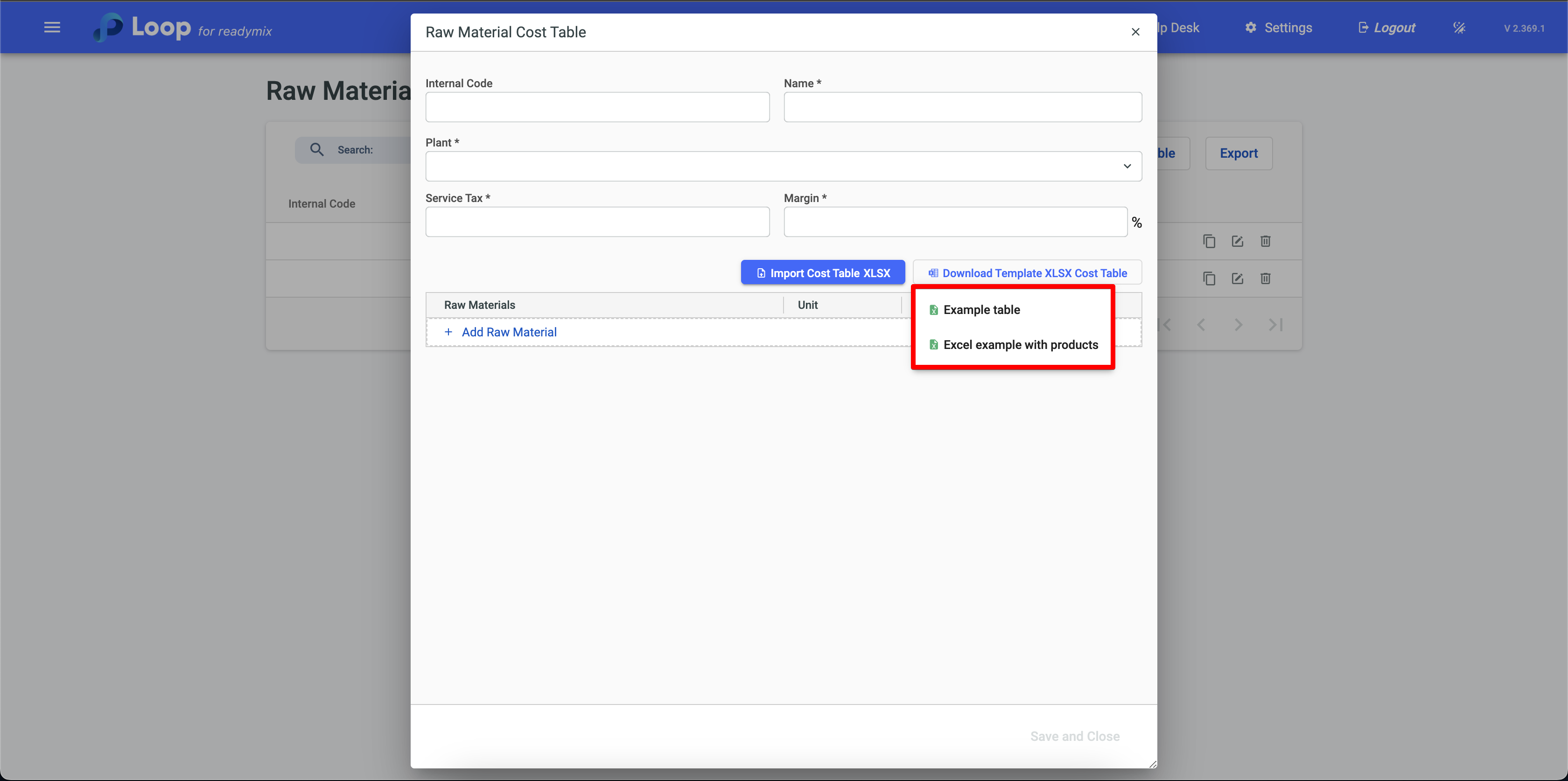
Import Cost Table
You can import data directly from an Excel spreadsheet into the cost table of the system, streamlining the update of prices and product details, ensuring that the information is always up to date and in sync with reality. To do this, simply go to the "Import Cost Table" option and select your spreadsheet.
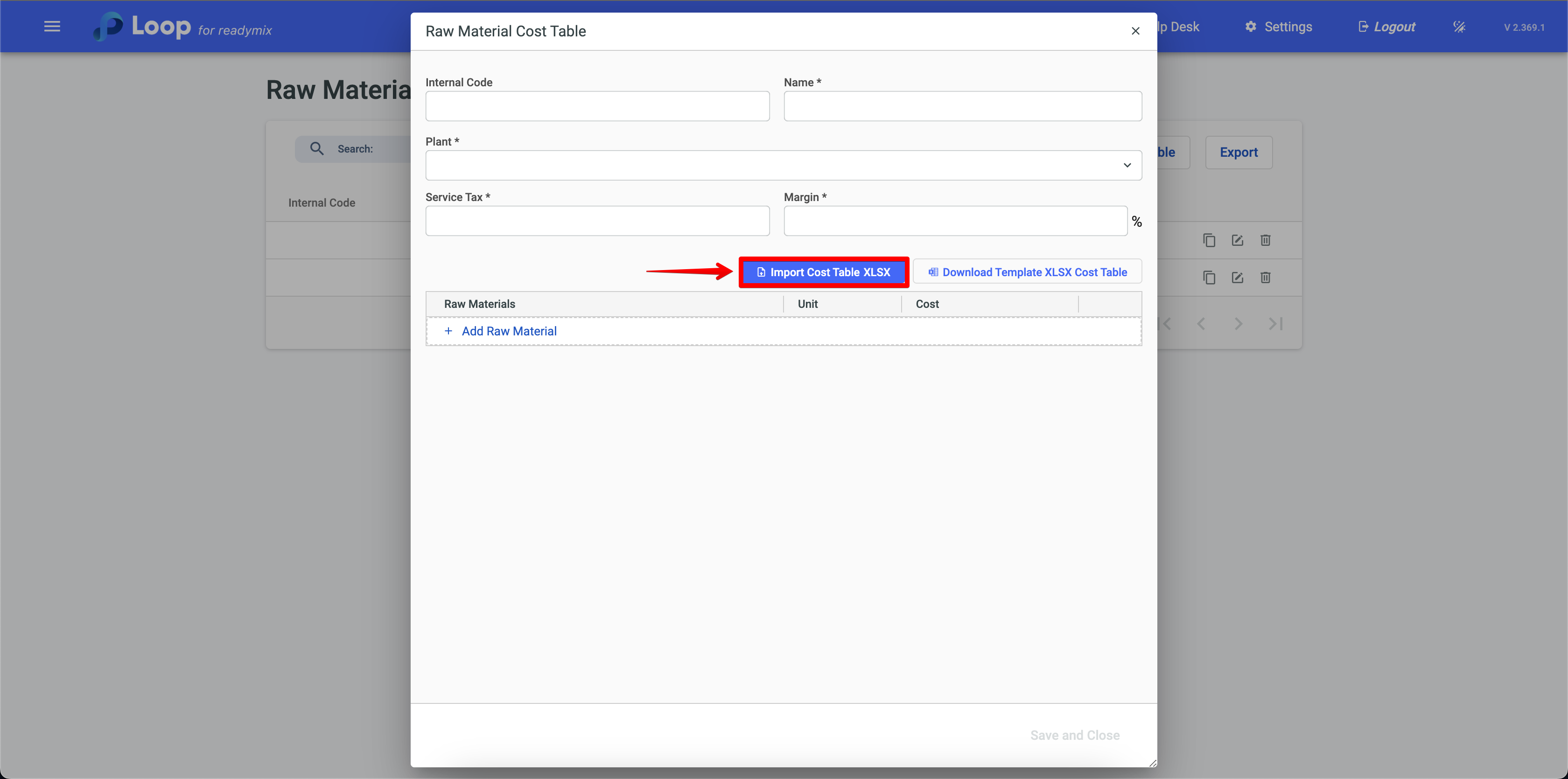
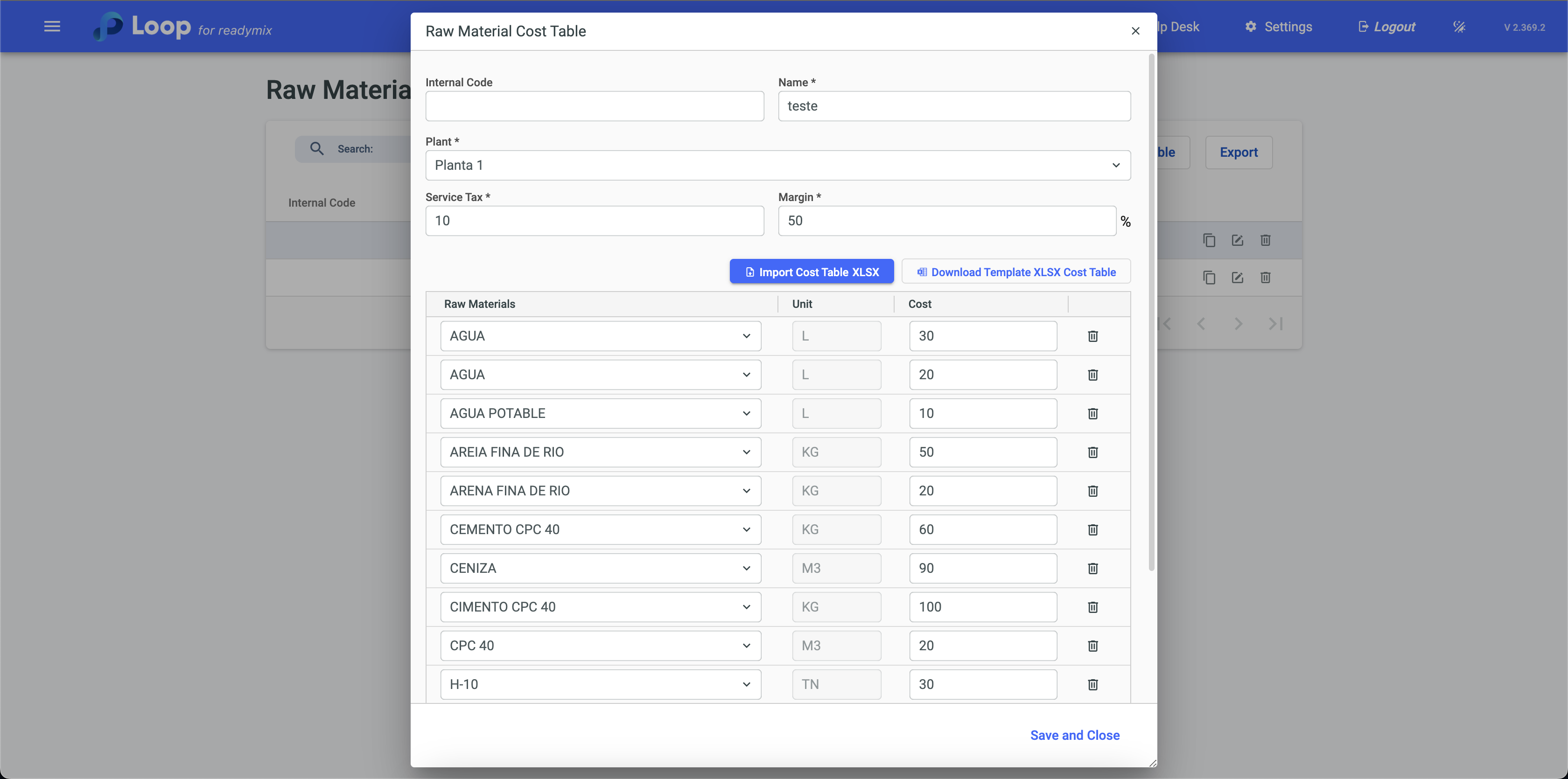
How to use
The price list plays a fundamental role in quickly and accurately calculating the costs of products, following their specific formulas. This functionality is evident on the "Formula Table" screen, where, when selecting a cost table, the system automatically calculates the total cost of the product. This ensures efficient management of production costs.

We can also view the product recipe and the detailed costs of each raw material used in the formulation. This allows precise control of inputs and the total cost of production, ensuring that all expenses are accounted for correctly to complete the recipe.

When adding a formula or configuring cost data, you can select a specific plant through the "Plant" field. This allows costs, margins and other information to be defined and applied to the chosen plant, customizing calculations according to the selected plant.

This definition is vitally important, because when a product is selected to create a new contract, the system automatically calculates the cost based on the updated prices of raw materials listed in the cost table. This ensures that production costs are accurately reflected in contracts, providing accurate and efficient financial management.

In this example, we observe a product whose price was updated based on the calculation of the product's MCC, using the previously filled cost table. With this tool, it is also possible to view the profit margin on the product, offering a clear and accurate view of profitability.